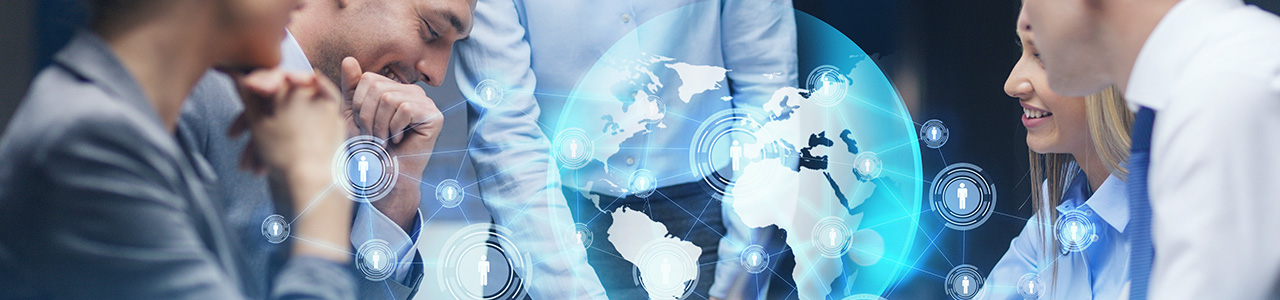
ETS Capability
- ETS can develop ESS with standardization and support engineering projects.
- ETS can perform maintenance service and quality opt checks at customer sites.
- ETS technicians can attend regular training sessions, then carry out installation, quality check and related takes nationwide under manufacturer’s guideline.
- ETS can warehouse ESS product and parts in designated locations; CA for West Coast, TX for South West, KY for Mid West/East Coast, and Toronto for Canada.
- ETS can inspect, monitor and maintain ESS product and parts in storage.
- ESS WMS system can periodically send data and activity reports to a manufacturer.
- EST CRM System can periodically send analytic data and reports to manufacturer.
- ETS CRM can generate RMA and assign filed support technicians to visit customer sites.
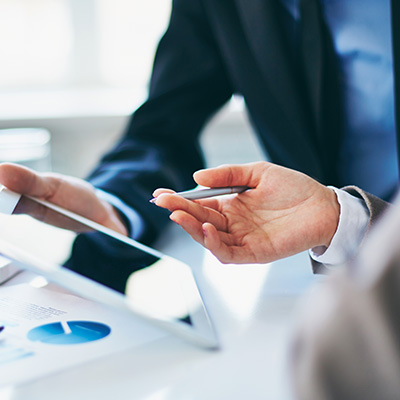
1. Operation Infra
- Real time monitoring and reporting for optimal site condition
- Parameter analysis and suggestion on usage patterns
- Pre-inspection before equipment operation
- Trouble-shooting/Safety manual provision
- Planning for training & maintenance
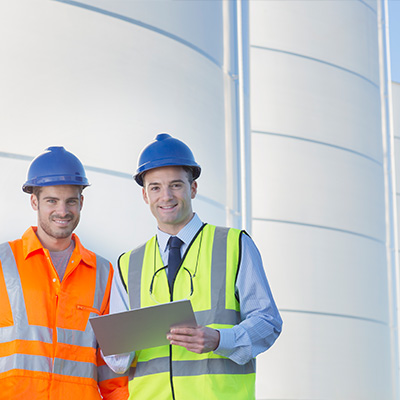
2. Facility Management
- Scheduled visit : Annual inspection visits
- Unscheduled visit : Visits upon customer request (Facility modifications, extra load, etc.)
- Reporting : Reporting of results of O&M visits Reporting on issues and improvement plans
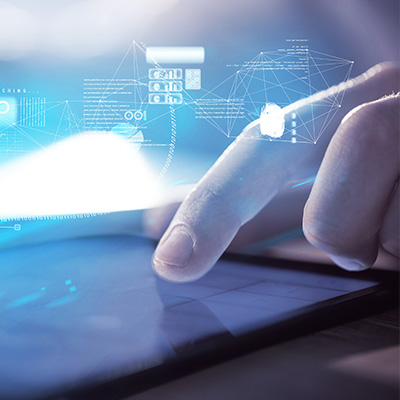
3. Analysis & Improvement
- Trouble shooting
- Repair & Replacement of defective components
- Spare parts management (quantity & update)
- VOC management: Immediate improvement upon receipt of VOC
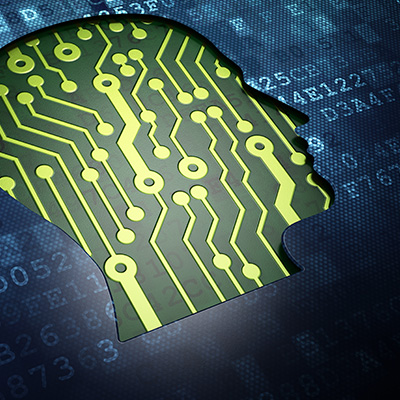
4. ETS CRM System
ETS CRM system can periodically send analytic data and reports to manufacturer.
ETS CRM can generate RMA and assign field support technicians to visit customer sites.